BLOG
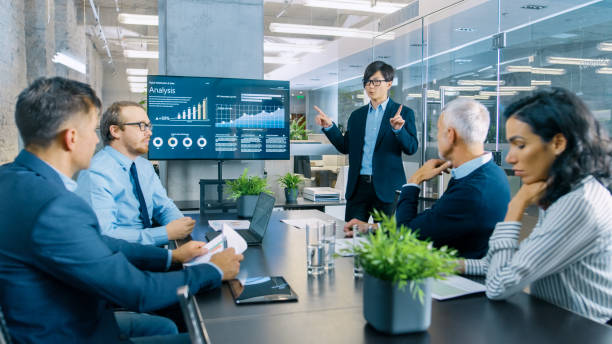
Yes! The future of sustainable manufacturing is heavily driven by technology. Innovations in automation, artificial intelligence (AI), Internet of Things (IoT), and advanced materials are making it possible to produce goods more efficiently while reducing waste and energy consumption. Some key trends shaping the future of sustainable manufacturing include:
1. Smart Factories & Industry 4.0
- IoT-enabled sensors for real-time monitoring and predictive maintenance
- AI-powered process optimization to reduce waste and improve efficiency
- Digital twins for virtual testing before physical production
2. Circular Economy & Recycling Tech
- Advanced recycling technologies to recover materials from waste
- Biodegradable and bio-based materials replacing traditional plastics
- Remanufacturing and refurbishment to extend product lifespans
3. Renewable Energy & Carbon Reduction
- Adoption of solar, wind, and hydro power in manufacturing facilities
- Carbon capture and utilization (CCU) to mitigate emissions
- Energy-efficient smart grids for optimized power use
4. 3D Printing & Additive Manufacturing
- On-demand production reducing material waste and transportation emissions
- Use of sustainable materials like recycled plastics and metal powders
- Lightweight design innovations for energy-efficient products
5. Green Chemistry & Sustainable Materials
- Development of non-toxic, biodegradable, and recyclable alternatives
- Innovations in waterless dyeing and eco-friendly coatings
- AI-driven material discovery to replace resource-intensive compounds
6. AI & Big Data for Sustainability
- AI-powered supply chain optimization to reduce transportation emissions
- Predictive analytics for better resource allocation and waste reduction
- Blockchain for transparent and ethical sourcing of materials
The convergence of these technologies is creating a more sustainable and resilient manufacturing industry. Do you have a specific area of interest within sustainable manufacturing, like a particular industry or technology?
Understanding the ground realities
Understanding the ground realities of sustainable manufacturing means looking beyond just the technological advancements and considering real-world challenges that companies face in implementation. While tech-driven sustainability is promising, businesses still struggle with factors like cost, infrastructure, and regulations. Here are some key ground realities:
1. High Initial Costs & ROI Concerns
- Investing in sustainable technologies (solar power, AI, automation) requires high upfront capital.
- Many small and mid-sized manufacturers lack funds or incentives to make the switch.
- ROI on green investments can take years, making businesses hesitant.
2. Skill Gap & Workforce Readiness
- Transitioning to Industry 4.0 needs skilled workers, but many factories still rely on traditional methods.
- Training programs for digital and sustainable manufacturing are not widespread.
3. Supply Chain & Raw Material Challenges
- Sustainable materials (biodegradable, recycled, or alternative components) can be expensive or scarce.
- Dependence on global supply chains makes it hard to ensure ethical sourcing.
- Logistics and transportation still contribute to carbon emissions.
4. Regulatory & Compliance Hurdles
- Governments worldwide are introducing stricter environmental regulations.
- However, policies vary widely, leading to confusion and inconsistencies.
- Compliance with green manufacturing standards adds paperwork and costs.
5. Resistance to Change
- Many industries, especially in developing economies, still operate on outdated models.
- Lack of awareness and fear of production disruptions slow down adoption.
- Traditional profit-driven mindsets often prioritize short-term gains over long-term sustainability.
6. Energy & Infrastructure Constraints
- Factories in regions with unreliable power grids struggle to adopt renewable energy.
- Infrastructure for recycling and waste management is underdeveloped in many countries.
- Sustainable manufacturing often requires new supply chain networks, which are not yet fully built.
7. Greenwashing & Lack of Transparency
- Some companies claim to be sustainable without real impact (greenwashing).
- Standardized, verifiable sustainability metrics are still evolving.
- Consumers and investors demand proof, but data collection is inconsistent.
Moving Forward: How to Bridge the Gap?
- Public & Private Collaboration: More incentives, subsidies, and tax benefits for green investments.
- Affordable Green Tech: Cheaper, scalable solutions tailored for smaller manufacturers.
- Education & Training: Upskilling workers to handle new technology.
- Localized Supply Chains: Encouraging regional sustainability networks.
- Transparent Data & Certification: Standardized sustainability metrics to combat greenwashing.
Despite the challenges, companies that adopt sustainable practices early will likely gain a competitive edge. Would you like insights on any specific industry or region?
Interconnected factories: A sustainable solution
Interconnected Factories: A Sustainable Solution
Interconnected factories—where multiple production units are linked through digital technology and data sharing—are emerging as a key strategy for sustainable manufacturing. This concept, often referred to as Smart Manufacturing or Industry 4.0, enables efficiency, resource optimization, and waste reduction by integrating IoT (Internet of Things), AI, cloud computing, and real-time analytics.
How Interconnected Factories Support Sustainability
1. Energy Optimization & Carbon Reduction
- Factories linked through smart grids can balance energy use, minimizing waste.
- AI-driven analytics help shift energy consumption to off-peak hours, reducing carbon footprint.
- Shared renewable energy sources (solar, wind) between factories lower reliance on fossil fuels.
2. Waste Reduction & Circular Manufacturing
- Factories can share excess materials instead of discarding them.
- AI-driven predictive analytics reduce overproduction and inventory waste.
- Inter-factory recycling networks ensure that scraps from one factory are repurposed in another.
3. Smart Supply Chains & Logistics
- Real-time data sharing among factories improves demand forecasting, reducing excess production.
- Smart routing and optimized transportation cut fuel consumption and emissions.
- AI-driven predictive maintenance minimizes machine failures and material losses.
4. Water & Resource Efficiency
- Factories can track and exchange water usage data, identifying leaks or inefficiencies.
- Shared treatment and recycling systems help reduce water waste.
- Blockchain transparency ensures responsible use of natural resources.
5. Resilient & Agile Manufacturing
- Interconnected factories can quickly shift production in response to disruptions (e.g., supply chain shortages).
- Companies can collaborate on on-demand manufacturing, reducing excess inventory and waste.
- Cloud-based systems allow remote monitoring and control, reducing unnecessary human travel.
Real-World Applications
🔹 Siemens & “Digital Twin” Factories
Siemens uses digital twins (virtual replicas) of interconnected factories to test sustainability strategies before real-world implementation.
🔹 Tesla’s Gigafactories
Tesla’s factories share data in real time, optimizing energy use and material efficiency across locations.
🔹 Airbus’ Smart Manufacturing Network
Airbus integrates AI-driven forecasting and real-time supply chain tracking to reduce production waste and optimize logistics.
Challenges & Considerations
⚡ High Initial Investment: Setting up interconnected systems requires advanced IoT infrastructure.
🛡 Cybersecurity Risks: More data sharing increases the risk of cyber threats.
🏭 Standardization Issues: Different factories may use incompatible systems, slowing integration.
📜 Regulatory Barriers: Cross-border factories must comply with different environmental laws.
Future Outlook
✅ 5G & Edge Computing will make real-time factory connectivity even faster and more reliable.
✅ AI-Driven Circular Economy will push interconnected factories to achieve near-zero waste.
✅ Decentralized Manufacturing Hubs will reduce transportation emissions by producing goods closer to demand.
Interconnected factories are a game-changer in sustainable manufacturing. The more industries adopt them, the closer we get to net-zero emissions and resource-efficient production.
Would you like insights on specific technologies or industries implementing this? 🚀
Examining the technology
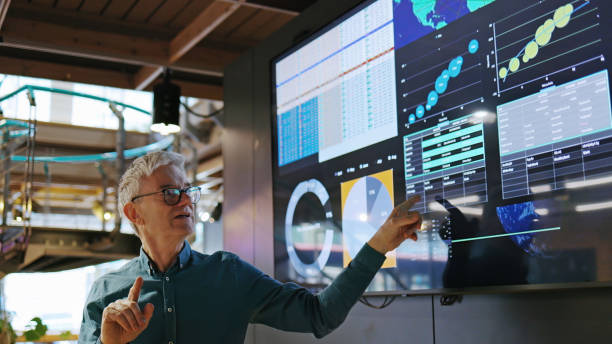
Examining the Technology Behind Interconnected Factories
Interconnected factories rely on cutting-edge digital technologies that enable real-time communication, automation, and sustainability. These technologies enhance efficiency, reduce waste, and optimize resources while driving the future of smart and sustainable manufacturing.
1. Industrial Internet of Things (IIoT) 🌐
IIoT connects machines, sensors, and systems to enable real-time data exchange.
🔹 Smart Sensors: Monitor energy consumption, emissions, and equipment health.
🔹 Digital Twins: Create virtual replicas of factories for simulation and optimization.
🔹 Automated Alerts: Detect faults and trigger preventive actions to reduce downtime.
✅ Example: General Electric (GE) uses IIoT to track machine performance and optimize energy usage in its factories.
2. Artificial Intelligence (AI) & Machine Learning (ML) 🤖
AI-powered systems analyze massive datasets to predict failures, optimize production, and enhance decision-making.
🔹 Predictive Maintenance: AI predicts machine breakdowns before they happen, reducing waste.
🔹 Process Optimization: AI fine-tunes production parameters to minimize material and energy usage.
🔹 Automated Quality Control: AI-driven vision systems detect defects, preventing waste.
✅ Example: Siemens’ MindSphere uses AI to analyze factory performance and optimize energy efficiency.
3. 5G & Edge Computing ⚡
High-speed connectivity ensures real-time data processing and minimal latency in factory operations.
🔹 Faster Machine-to-Machine Communication: Enables seamless coordination between factory units.
🔹 Edge Computing: Processes data closer to the source, reducing cloud dependency and energy use.
🔹 Remote Monitoring & Control: Enables factory management from anywhere.
✅ Example: Ericsson & Hitachi use 5G-enabled smart factories to monitor and control operations remotely.
4. Cloud Computing & Big Data ☁️
Cloud-based platforms allow factories to store, analyze, and share operational data for improved efficiency.
🔹 Centralized Data Management: Factories can access shared sustainability reports and benchmarks.
🔹 AI-Driven Analytics: Cloud systems process vast amounts of data for optimization insights.
🔹 Scalability: Factories can expand and integrate new systems easily.
✅ Example: Amazon Web Services (AWS) provides cloud solutions for manufacturers to optimize supply chains.
5. Blockchain for Supply Chain Transparency 🔗
Blockchain ensures secure and transparent tracking of raw materials and emissions across factories.
🔹 Real-Time Material Tracking: Factories can ensure ethical and sustainable sourcing.
🔹 Smart Contracts: Automates transactions and compliance verification.
🔹 Immutable Records: Prevents greenwashing by providing verifiable sustainability data.
✅ Example: IBM Blockchain helps track and verify sustainable materials in the automotive and textile industries.
6. Robotics & Automation 🤖⚙️
Smart robots streamline processes while reducing resource consumption.
🔹 Collaborative Robots (Cobots): Work alongside humans to improve precision and efficiency.
🔹 Automated Guided Vehicles (AGVs): Transport materials with minimal energy consumption.
🔹 Adaptive Manufacturing Systems: Machines adjust to real-time demand, reducing overproduction.
✅ Example: Tesla’s Gigafactories use AI-powered robots for high-efficiency, low-waste production.
7. Additive Manufacturing (3D Printing) 🖨️
3D printing minimizes waste by using on-demand, layer-by-layer production.
🔹 Material Efficiency: Reduces scrap material by up to 90%.
🔹 Lightweight Components: Produces optimized designs with less material.
🔹 Localized Production: Cuts transportation emissions.
✅ Example: Airbus uses 3D printing to create aircraft parts, reducing waste and improving sustainability.
The Future of Interconnected Factories 🚀
🔹 AI-driven self-optimizing factories with minimal human intervention.
🔹 Decentralized & modular production to reduce supply chain risks.
🔹 Zero-carbon manufacturing with 100% renewable-powered smart grids.
Conclusion
Interconnected factories aren’t just a vision—they are already transforming industries by making manufacturing smarter, cleaner, and more sustainable.
Would you like insights on specific case studies or implementation strategies? 🤔
Also Read: 7 approaches for sustainable manufacturing growth
Here are seven key approaches for achieving sustainable manufacturing growth:
1. Energy Efficiency & Renewable Integration ⚡🌱
🔹 Optimize energy use with AI-driven energy management.
🔹 Adopt solar, wind, and hydro power to reduce reliance on fossil fuels.
🔹 Implement smart grids to balance energy demand across interconnected factories.
✅ Example: Siemens integrates AI-based energy monitoring in its factories, reducing energy waste by 20%.
2. Circular Economy & Zero Waste Strategy 🔄♻️
🔹 Design for reuse & recycling – extend product life cycles.
🔹 Use biodegradable, recycled, or remanufactured materials.
🔹 Implement waste-to-energy solutions and closed-loop recycling.
✅ Example: Patagonia promotes a repair-and-reuse model to extend the lifespan of its products.
3. Smart & Digital Manufacturing (Industry 4.0) 🏭🤖
🔹 Use IoT, AI, and cloud computing for real-time monitoring and optimization.
🔹 Enable predictive maintenance to reduce downtime and material waste.
🔹 Implement digital twins to simulate and improve manufacturing processes.
✅ Example: GE’s Brilliant Factories use AI-driven predictive analytics to cut resource waste.
4. Sustainable Supply Chains & Green Logistics 🚚🌍
🔹 Optimize transportation routes to reduce fuel consumption & emissions.
🔹 Source materials locally and ethically to minimize carbon footprints.
🔹 Implement blockchain for transparent, eco-friendly procurement.
✅ Example: Unilever reduced emissions by 40% by optimizing its supply chain logistics.
5. Water Conservation & Eco-Friendly Processes 💧🔬
🔹 Deploy AI-based water monitoring to track and minimize usage.
🔹 Reuse and treat wastewater through advanced filtration systems.
🔹 Use waterless dyeing & chemical-free production methods.
✅ Example: Levi’s Water<Less® initiative reduced water use by over 3 billion liters.
6. Sustainable Materials & Green Chemistry 🏗️🌿
🔹 Develop bio-based plastics, alternative metals, and composites.
🔹 Reduce toxic chemicals and shift to eco-friendly coatings & adhesives.
🔹 Use lightweight, durable materials to improve energy efficiency in products.
✅ Example: Ford incorporates bio-based materials like soy foam in its car interiors.
7. Policy Compliance & Green Certifications 📜✅
🔹 Adopt ISO 14001 and LEED certifications for sustainable operations.
🔹 Align with government incentives & carbon neutrality goals.
🔹 Implement corporate sustainability reporting for accountability.
✅ Example: Apple aims for carbon neutrality across its entire supply chain by 2030.
Final Thoughts 💡
By combining these seven approaches, manufacturers can reduce costs, enhance efficiency, and contribute to a sustainable future.
Would you like me to expand on any specific area or provide real-world case studies? 🚀
Embracing the future
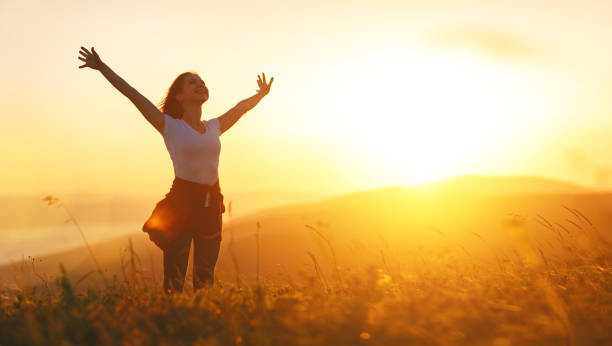
Embracing the Future of Sustainable Manufacturing 🚀🌍
The manufacturing industry is at a turning point—embracing technology-driven sustainability is no longer optional but necessary for long-term growth. Interconnected factories, AI-driven optimization, circular economy models, and renewable energy are transforming the landscape, making manufacturing more efficient, resilient, and eco-friendly.
1. The Shift to Smart & Sustainable Factories 🏭💡
🔹 Industry 4.0: IoT, AI, and automation are making factories smarter and less resource-intensive.
🔹 Digital Twins: Virtual simulations help optimize production before using real-world resources.
🔹 Predictive Maintenance: AI minimizes waste and downtime by forecasting equipment failures.
✅ Example: Siemens’ MindSphere uses cloud-based AI to optimize industrial energy efficiency.
2. The Circular Economy Revolution 🔄♻️
🔹 Closed-loop manufacturing: Designing products to be reused, remanufactured, or recycled.
🔹 Material innovation: Bio-based plastics, recycled metals, and low-carbon composites.
🔹 Zero-waste production: Advanced sorting, recycling, and repurposing of materials.
✅ Example: Nike’s Move to Zero uses recycled materials to reduce waste and carbon emissions.
3. Net-Zero & Carbon-Neutral Goals 🌱⚡
🔹 Renewable energy integration: Solar, wind, and green hydrogen powering factories.
🔹 Smart energy grids: AI-driven energy distribution to cut emissions.
🔹 Carbon capture technologies: Factories turning emissions into usable materials.
✅ Example: Tesla Gigafactories operate on renewable energy, reducing carbon impact.
4. AI & Big Data for Decision-Making 🤖📊
🔹 AI-powered supply chains: Reducing overproduction and unnecessary waste.
🔹 Blockchain for transparency: Ensuring ethical, sustainable sourcing of materials.
🔹 Real-time analytics: Monitoring emissions, energy usage, and environmental impact.
✅ Example: Unilever’s AI-driven logistics system cut transportation emissions by 40%.
5. Collaboration & Policy Support 🤝📜
🔹 Public-private partnerships: Governments supporting industries with green incentives.
🔹 Global sustainability goals: Compliance with Paris Agreement & UN SDGs.
🔹 Green certifications & accountability: ISO 14001, LEED, and carbon neutrality pledges.
✅ Example: Apple’s supply chain aims for 100% carbon neutrality by 2030.
Final Thoughts: The Future is Now 🌍🔮
The transition to sustainable manufacturing is already happening—businesses that embrace these technologies will lead the next industrial revolution. Automation, AI, renewable energy, and closed-loop production will define the factories of the future.
Would you like insights on implementation strategies or a specific industry’s approach? 🚀
Also Read: How govt can create sustainable manufacturing growth in India
How the Government Can Drive Sustainable Manufacturing Growth in India 🇮🇳🌱
India is at a critical juncture in its industrial growth, and government policies play a crucial role in ensuring that manufacturing expands sustainably. By leveraging policy reforms, green incentives, and digital transformation, the government can create an ecosystem where industries thrive while minimizing environmental impact.
1. Green Incentives & Financial Support 💰🌿
🔹 Subsidies & Tax Benefits: Provide tax rebates on renewable energy adoption, energy-efficient machinery, and green manufacturing practices.
🔹 Low-Interest Green Loans: Offer special financing schemes for MSMEs investing in sustainability.
🔹 Carbon Credit Trading: Encourage industries to offset emissions by investing in clean energy projects.
✅ Example: India’s Production-Linked Incentive (PLI) Scheme for electric vehicles and renewable energy manufacturing.
2. Renewable Energy & Smart Grids ⚡🔋
🔹 Expand Solar & Wind Power Integration: Incentivize industries to adopt solar rooftops and captive wind farms.
🔹 Green Hydrogen Adoption: Promote the use of hydrogen as a clean energy source for heavy industries.
🔹 Smart Energy Management Systems: Implement AI-driven energy grids to optimize factory power consumption.
✅ Example: India’s National Hydrogen Mission aims to make the country a global hub for green hydrogen production.
3. Circular Economy & Waste Management 🔄♻️
🔹 EPR (Extended Producer Responsibility) Regulations: Ensure manufacturers take responsibility for product end-of-life recycling.
🔹 Zero-Waste Manufacturing Policies: Enforce material recovery and reusability in industries.
🔹 Waste-to-Energy Incentives: Support factories in converting industrial waste into energy sources.
✅ Example: The Swachh Bharat Mission has already improved solid waste management practices in urban industries.
4. Digital & Smart Manufacturing (Industry 4.0) 🏭🤖
🔹 Adoption Grants for AI & IoT: Provide funding for smart factory transformations.
🔹 National AI & Robotics Strategy: Develop AI-driven sustainable manufacturing clusters.
🔹 Digital Skill Development Programs: Train workers in data-driven production efficiency.
✅ Example: NITI Aayog’s AI Strategy promotes automation for sustainable industrial growth.
5. Sustainable Supply Chains & Green Logistics 🚚🌍
🔹 Rail & Water Transport Subsidies: Shift industrial transportation from road to rail/water to cut emissions.
🔹 Green Infrastructure: Develop low-carbon industrial zones with sustainable transport connectivity.
🔹 Blockchain for Supply Chain Transparency: Ensure ethical and sustainable sourcing of raw materials.
✅ Example: The Dedicated Freight Corridor (DFC) Project aims to create efficient and green transport corridors for industries.
6. Green Certifications & Compliance 📜✅
🔹 Mandatory ESG (Environmental, Social, Governance) Reporting for large corporations.
🔹 ISO 14001 & Green Factory Standards: Encourage companies to adopt international sustainability benchmarks.
🔹 Carbon Tax Implementation: Penalize high-carbon industries while rewarding low-emission manufacturers.
✅ Example: The Perform, Achieve & Trade (PAT) Scheme has successfully reduced industrial energy consumption in India.
7. Public-Private Collaboration for R&D & Innovation 🏛️🤝
🔹 Government-Industry Research Partnerships: Create innovation hubs for sustainable materials and energy solutions.
🔹 Startup & MSME Support: Provide seed funding for cleantech startups and SMEs working on green manufacturing.
🔹 University-Industry Collaborations: Encourage academic research in sustainable production technologies.
✅ Example: The Atal Innovation Mission (AIM) fosters industrial innovation, including sustainability-focused projects.
Final Thoughts: A Green Roadmap for India 🇮🇳🌏
With strong policy direction, financial incentives, and technological integration, the Indian government can drive sustainable manufacturing growth while making India a global leader in green industries.
Would you like insights on specific policy recommendations or industry case studies? 🚀